In the world of manufacturing and assembly, measurement of torque tightening of fasteners is imperative for the effectiveness of production and product quality. On one hand, loose attachment may vibrate or loosen, on the other hand if the torque is too high a bold can break. Faced with these problems, manufacturers are realizing that a well-managed torque system can make the difference between a safe, reliable, economic product and a complete disaster.
The main tools used in industry to ensure quality of the screwing process, are torque screwdrivers and torque wrenches. However these tools or instruments themselves need to be checked regularly to ensure the tightening and accuracy of the measurement. Generally, these audits are performed periodically (e.g. once a year) to ensure proper correspondence between the torque setting and the actual value. The tools are then sent to a laboratory responsible for carrying out calibrations.
Today, the quality of products must be better and better, it is therefore become necessary to increase the frequency of verifications. These verifications dramatically increase the costs of calibration, mainly when it is done by an outside laboratory. But these verifications can also be done internally for almost no cost using a Torque analyzer. The use of a torque analyzer is an effective, fast, reliable method for torque calibration.
1. What is a torque analyzer?
A torque analyzer is actually a reference torque gauge used to measure the torque of a tightening tool. Torque analyzers are compounds of:
- A static torque sensor calibrated with a certificate of calibration linked to national standards (NIST for example). This sensor must be more accurate than the tools to control (0.5% is a good compromise).
- A display with features tailored to specific measures verification: internal memory, breaking up, tracking ...
2. Torque wrench and screwdriver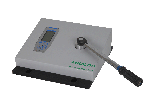
Torque wrench and torque screwdrivers are adjustable tools used for tightening. They are triggered when the torque value is reached. They generally have an accuracy between 2 and 5%.
The verification of these tools requires the use of break feature in the torque analyzer. It facilitates measures as wrenches or screwdrivers continue to apply torque after triggering. Break feature of the analyzer can detect and keep in memory this trigger value. Analyzers equipped with only peak feature are not appropriate and make this type of control.
3. Torque wrenches with continuous measurement
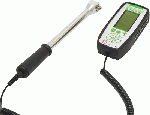
Some torque wrenches can be equipped with a display that allows real-time torque reading. They generally have a peak memory feature. These wrenches are used to measure and verify the torque directly on the floor in both directions.
For the calibration of these tools or instrument, the torque analyzer must have a real time display of the torque value. This measurement is relatively difficult because the values are varying all the time. It is also possible to compare the maximum identified by the two devices. However, the accuracy of this measurement is strongly dependent on the speed acquisition devices.
The best solution is to use deadweights with a torque bar to calibrate this type of torque gauges.
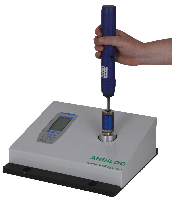
4. Verification of powered screwdrivers
The analyzers also allow torque control of powered screwdrivers. To do this, make sure of two things:
- The acquisition speed of the torque analyzer torque is high (1000 Hz) to ensure that the analyzer measures properly
- You can use a rundown adapter on the static torque sensor. Indeed, the torque sensor analyzers do not allow the screwdriver to rotate.